Optimizing master data is non-negotiable. Two fundamental yet distinct practices—service code material standardization lie at the heart of operational and financial efficiency.
Despite sounding technical, these processes significantly impact your bottom line, whether you’re managing pipelines, ports, hospitals, or high-rise construction. This article explores the key differences, benefits, challenges, and regional relevance of service code material standardization.
What is Service Code Creation?
Service codes represent structured identifiers for intangible activities performed by vendors or internal teams ranging from annual maintenance to asset inspection.
Key attributes include:
- Service description
- Unit of measurement (UOM)
- Pricing mechanism
- SLA and compliance elements
By applying service code material standardization, organizations avoid billing errors, gain procurement clarity, and boost vendor performance tracking.
What is Material Code Standardization?
Material codes refer to physical items like tools, equipment, or raw materials. Over time, duplicate or inconsistent entries degrade data quality, leading to overstocking and procurement inefficiencies.
Key components:
- Noun-modifier description logic
- Standard units of measure
- Industry classification (e.g., UNSPSC, eCl@ss)
- Manufacturer part numbers (MPNs)
Implementing service code material standardization helps reduce cost, streamline inventory, and eliminate duplication across ERPs.
Key Differences: Service Code vs Material Standardization
Criteria | Service Code Creation | Material Code Standardization |
---|---|---|
Focus | Intangible services | Tangible materials |
Purpose | Procurement control for services | Data consistency for materials |
Common Users | Maintenance, Procurement, Finance | Engineering, Stores, SCM |
Typical Fields | Task, SLA, UOM, Rate | Specs, MPN, Category, Description |
Impact | Visibility & compliance | Inventory accuracy & spend reduction |
Both are essential and interlinked. Service code material standardization is most effective when implemented across services and materials together.
Industry Use Cases
Oil & Gas
- Service Code: ROV inspections, pipeline repair
- Material Code: Valves, actuators, flanges
Helps manage large-scale vendor scopes and avoid duplicate item entries across rigs or refineries.
Utilities
- Service Code: Line inspection, emergency restoration
- Material Code: Insulators, cable drums
Aids in accurate contractor billing and asset traceability.
Real Estate & Construction
- Service Code: Subcontractor labor, civil inspections
- Material Code: Concrete grades, wiring kits
Prevents miscommunication in BoQ vs actuals, aiding project tracking.
Healthcare & Lifesciences
- Service Code: Facility sterilization, MRI calibration
- Material Code: Gloves, syringes, ventilators
Supports regulatory audits and prevents stockouts of critical items.
EPC Projects
- Service Code: Site surveys, safety audits
- Material Code: Electrical panels, mechanical fittings
Reduces turnaround time and boosts compliance across international projects.
Common Challenges & How to Overcome Them
Challenge | Solution |
---|---|
Fragmented data across sites or regions | Centralized MDM platform with governance workflows |
No clear ownership of service descriptions | Appoint service data stewards and create approval flows |
Duplication due to free text entries | Enforce structured templates and AI validation checks |
Lack of industry standards | Map to eCl@ss, UNSPSC, or domain-specific taxonomies |
User resistance to change | Educate teams with ROI-backed training programs |
Overcoming these issues with service code material standardization sets the stage for scalable digital transformation.
ROI & KPIs to Track
Organizations adopting service code material standardization see measurable impact.
Key ROI Drivers:
- Reduced procurement cycle times
- Decreased working capital from inventory reduction
- Fewer invoice disputes or errors
- Better contract compliance
Suggested KPIs:
- % of duplicate materials/services eliminated
- Procurement accuracy rate
- Working capital saved via inventory optimization
- Vendor performance metrics (SLA adherence, response time)
Technology That Enables It
Several platforms and technologies now simplify service code material standardization.
- AI-based Deduplication Engines
Identify duplicates, inconsistencies, and misclassified entries in real-time. - Standardized Taxonomy Libraries
Support eCl@ss, UNSPSC, ISO 8000, etc., for classification consistency. - MDM Platforms (like PROSOL)
Provide end-to-end master data governance, from creation to approval and integration into SAP, Oracle, Maximo, and more. - Data Quality Dashboards
Visualize improvements, spot gaps, and track governance workflows.
Why You Need Both
Focusing only on services or materials creates blind spots. Integrating service code material standardization delivers:
- Better analytics across spend categories
- Accurate work order and job costing
- Streamlined asset management and CMMS integration
- Predictable maintenance and shutdown planning
Implementation Best Practices
For Service Codes
- Start with top 100 recurring services
- Link codes to contract SLAs
- Avoid free-text during purchase requisitions
For Materials
- Validate new codes against master list
- Involve OEMs for part descriptions
- Standardize UOMs (e.g., meters vs mtr)
A governance council with representation from procurement, maintenance, finance, and IT ensures long-term success.
Need help with cleaning up your service data? Get a personalized report on your current master data quality.
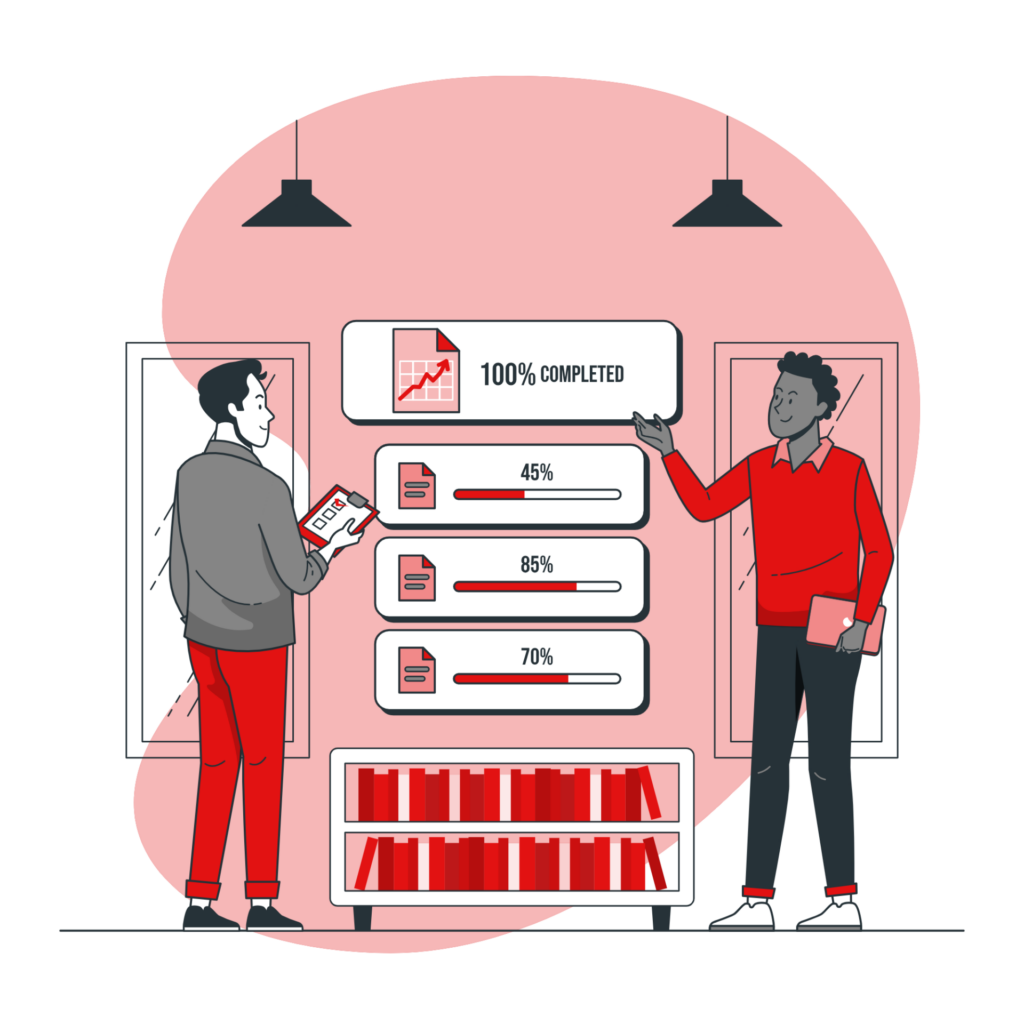
Frequently Asked Questions
Q1: What is service code material standardization?
It’s a unified approach to cleanse, structure, and manage both service and material master data for better procurement, compliance, and reporting.
Q2: Can I use one framework for both?
Yes. A central data governance model supports consistency, accuracy, and accountability across both data types.
Q3: How often should codes be updated?
Quarterly or whenever there are major vendor or project changes.
Q4: Does this apply to small businesses too?
Absolutely. Small teams can benefit from simplified templates and faster procurement cycles.
Q5: What tools can help?
MDM platforms like PROSOL, taxonomy libraries (e.g., eCl@ss), and AI-powered deduplication engines.
Final Thoughts
Whether you’re managing inventories in Mumbai, project sites in Muscat, or hospital assets in Singapore, a unified service code material standardization strategy is your competitive edge. It ensures data accuracy, drives procurement efficiency, and unlocks true business intelligence.