Every hour of unexpected downtime costs industries millions. Whether you’re managing an oil refinery in Kuwait, a hospital in India, or a manufacturing plant in Vietnam, the reality remains the same: reactive maintenance is expensive and unsustainable. This blog post explores how RCM can revolutionize asset management practices in the manufacturing sector.
Extending the life of critical assets is a survival strategy. This is where Reliability-Centered Maintenance (RCM) steps in, offering a powerful blueprint for transforming maintenance programs and ensuring asset longevity.
By embracing RCM for asset longevity, businesses in India, GCC (UAE, Saudi Arabia, Qatar, Oman, Kuwait, Bahrain), and the Far East (China, Japan, Singapore, and beyond) are protecting their investments and building more resilient operations.
What is RCM for Asset Longevity?
Reliability-Centered Maintenance (RCM) is a structured, analytical process that identifies how assets fail and develops proactive strategies to prevent those failures.
Instead of running equipment until it breaks (and then scrambling to fix it), RCM ensures that maintenance is:
- Planned
- Strategic
- Cost-effective
In short, RCM for asset longevity focuses on maintaining an asset’s intended functions for as long as possible, maximizing its return on investment.
Core Elements of RCM:
- Functional Failure Analysis: What happens when the asset fails?
- Failure Modes and Effects Analysis (FMEA): What causes failures and how severe are they?
- Maintenance Task Selection: Which tasks best prevent or detect failure?
- Maintenance Strategy Implementation: How can we execute the right interventions at the right time?
Important:
RCM doesn’t mean more maintenance.
It means smarter maintenance, doing the right work at the right time.
Why Industries Can No Longer Rely on Reactive Maintenance
Many businesses still wait for a machine to fail before taking action.
However, this “break-fix” mindset comes at a heavy price:
Problem | Consequence |
---|---|
Frequent Equipment Breakdowns | Higher repair and replacement costs |
Unplanned Downtime | Lost production and missed deadlines |
Increased Safety Risks | More accidents and compliance violations |
Shortened Asset Life | Higher capital expenditure (CAPEX) |
Negative Environmental Impact | Increased carbon footprint |
Example:
An offshore oil platform in Oman recently lost $8.5 million due to an unplanned pump failure that could have been prevented with simple RCM principles.
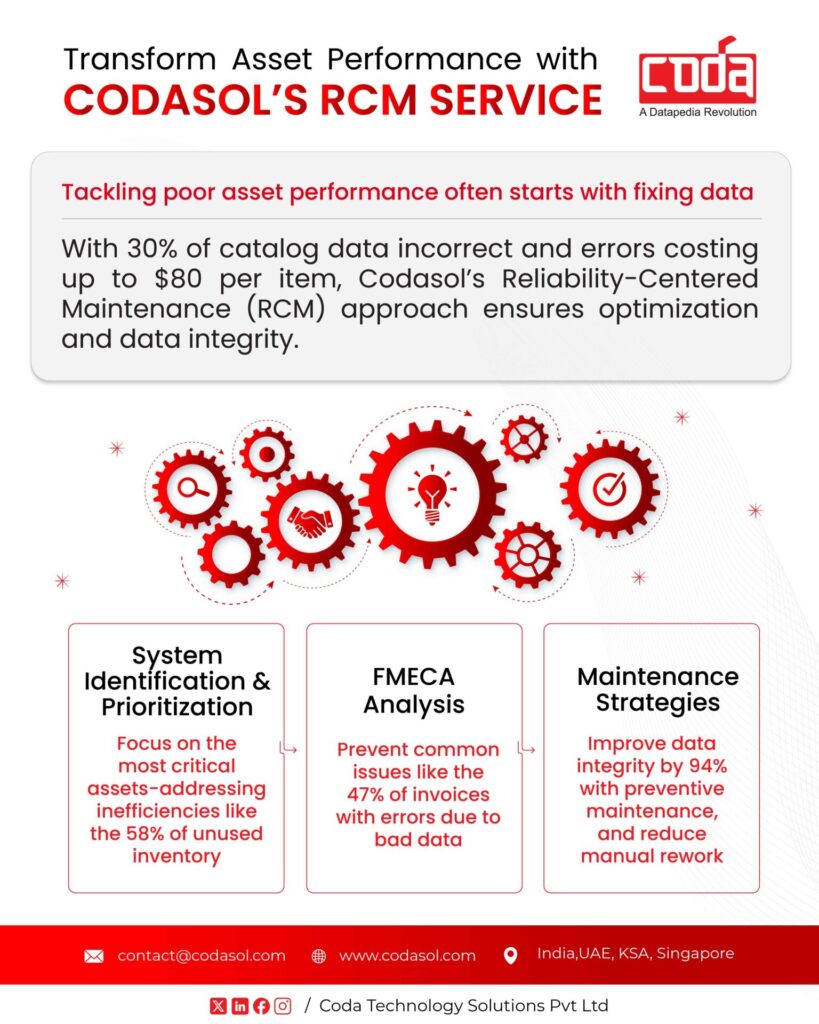
Top 7 Benefits of RCM for Asset Longevity
Implementing RCM unlocks tangible and measurable benefits across industries:
Benefit | Details |
---|---|
Reduced Downtime | Scheduled maintenance minimizes unexpected failures |
Lower Maintenance Costs | Predictive tasks prevent costly emergency repairs |
Extended Asset Lifespan | Assets perform reliably for longer |
Enhanced Safety | Addressing risks proactively safeguards people |
Increased Operational Efficiency | Smooth operations drive higher output |
Environmental Protection | Prevent leaks, spills, and energy waste |
Better Budget Control | Predictable maintenance expenses improve financial planning |
Across India, the GCC, and the Far East, businesses implementing RCM for asset longevity have reported cost savings ranging from 15% to 40%.
Switch to proactive maintenance today and save millions in downtime costs.
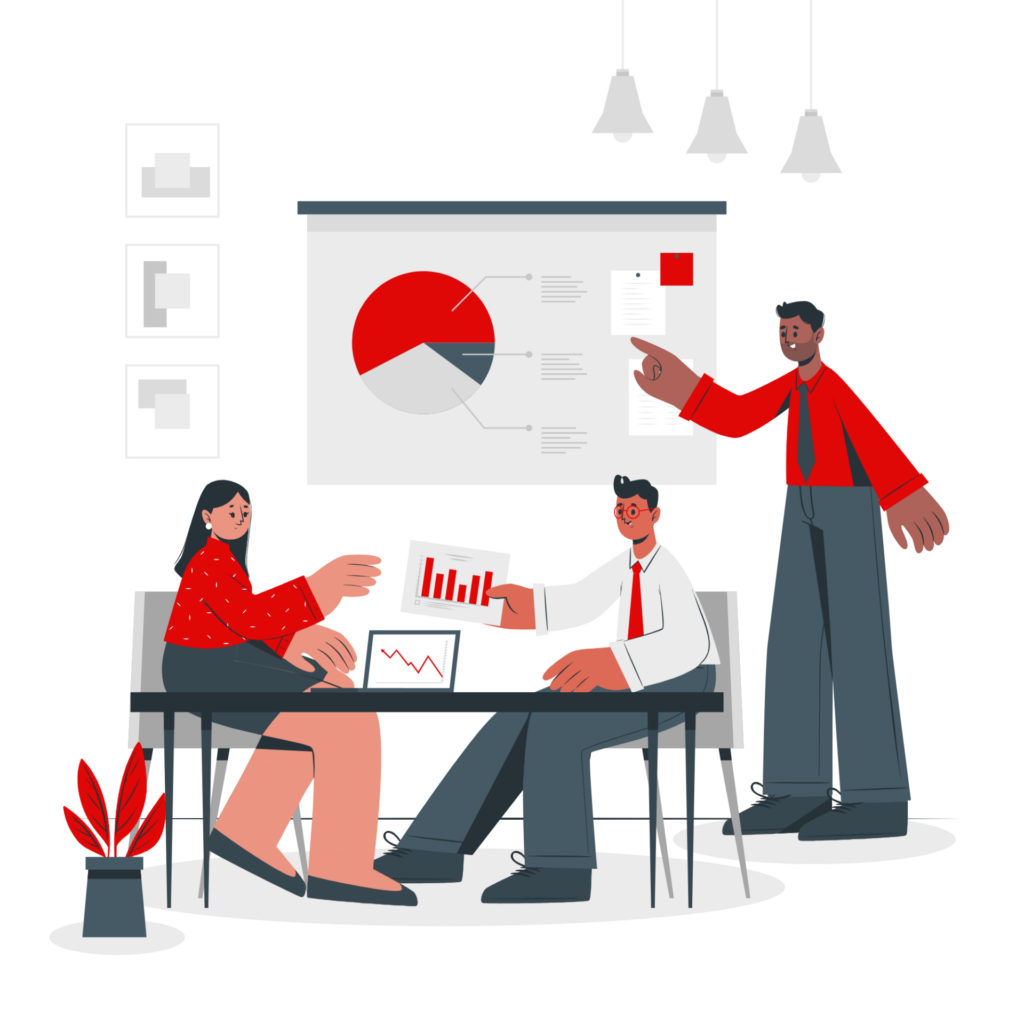
Step-by-Step Guide: How to Implement RCM for Asset Longevity
Successfully deploying RCM requires a clear plan. Follow these five steps to ensure your success:
Step 1: Identify Critical Assets
Focus on assets whose failure would have the biggest impact on safety, operations, or the environment.
Example:
In a hospital in Singapore, MRI machines and surgical equipment are prime candidates for RCM.
Step 2: Conduct Failure Modes and Effects Analysis (FMEA)
Analyze:
- How assets can fail
- Why they fail
- What the consequences are
Use these insights to design targeted preventive actions.
Step 3: Develop Maintenance Strategies
Choose from four types of maintenance:
- Preventive Maintenance (scheduled inspections)
- Predictive Maintenance (condition monitoring)
- Detective Maintenance (finding hidden failures)
- Run-to-Failure (only for non-critical assets)
Step 4: Train and Engage Staff
RCM requires a mindset shift across your workforce.
Invest in training programs to equip your teams with RCM skills and knowledge.
Step 5: Monitor, Review, and Improve
Implement KPIs to track performance.
Continuously refine your maintenance strategies based on real-world results.
How Different Industries Use RCM for Asset Longevity
Oil & Gas
- RCM prevents catastrophic failures in offshore platforms and pipelines.
- Saudi Aramco cut downtime by 35% with RCM-driven strategies.
Utilities
- Power grids in the UAE rely on predictive analytics to prevent blackouts.
- Water treatment plants optimize pump performance with early detection programs.
Manufacturing
- Factories in India use vibration monitoring on critical machines to reduce breakdowns.
- Automotive plants in Thailand extend press machine life by 5+ years through preventive tasks.
Healthcare
- Hospitals in Singapore use RCM to maintain critical imaging and life-support systems, ensuring patient safety.
Aviation
- Airlines in Qatar and Japan apply RCM to maintain aircraft airworthiness and reduce costly AOG (Aircraft on Ground) incidents.
Construction, Ports, Banking, and Defense
Every industry, from real estate to defense forces, can leverage RCM for asset longevity to lower operational risks and maximize asset value.
Challenges in Implementing RCM (And How to Overcome Them)
While RCM brings many benefits, challenges do exist:
Challenge | Solution |
---|---|
Resistance to Change | Build awareness with leadership support and success stories |
Lack of Expertise | Invest in RCM training and partner with experienced consultants |
High Initial Costs | Focus on critical assets first; savings will fund expansion |
Data Management Issues | Use CMMS (Computerized Maintenance Management Systems) and IoT sensors |
Cultural Barriers | Promote a culture of reliability through regular workshops |
What’s Next for RCM and Asset Management?
- AI and Machine Learning: Predict failures with unprecedented accuracy.
- IoT-Enabled Assets: Real-time monitoring of health and performance.
- Sustainability Integration: RCM supports ESG goals by minimizing environmental damage.
- Autonomous Maintenance: Workers partner with smart systems for higher efficiency.
Industries adopting RCM for asset longevity are building future-proof operations capable of weathering economic, environmental, and operational storms.
FAQ Section
Q1: What exactly is RCM for asset longevity?
RCM for asset longevity means using Reliability-Centered Maintenance strategies to keep assets functioning properly for as long as possible, reducing downtime and costs.
Q2: How is RCM different from traditional maintenance?
Traditional maintenance often relies on routine tasks or emergency fixes. RCM, in contrast, uses data-driven analysis to prioritize the right maintenance at the right time.
Q3: Can small and medium businesses (SMBs) implement RCM?
Absolutely! Even small manufacturers, hospitals, and service providers can tailor RCM programs to fit their resources and needs.
Q4: What is the ROI of implementing RCM?
Depending on industry and scale, ROI can range from 300% to 600% within 12–18 months through cost savings, efficiency gains, and extended asset life.
Q5: How long does it take to see results from RCM?
Early improvements often appear within the first 3–6 months. Full optimization typically takes 12–24 months, depending on organizational size and complexity.
Final Thoughts:
If you’re serious about cutting downtime, reducing costs, and achieving sustainable growth, it’s time to leave reactive maintenance behind.
By adopting RCM for asset longevity, industries across India, GCC, and the Far East are future-proofing their operations, empowering their people, and protecting their profits.
The longer you wait, the more you’re losing.
Start your RCM journey today.
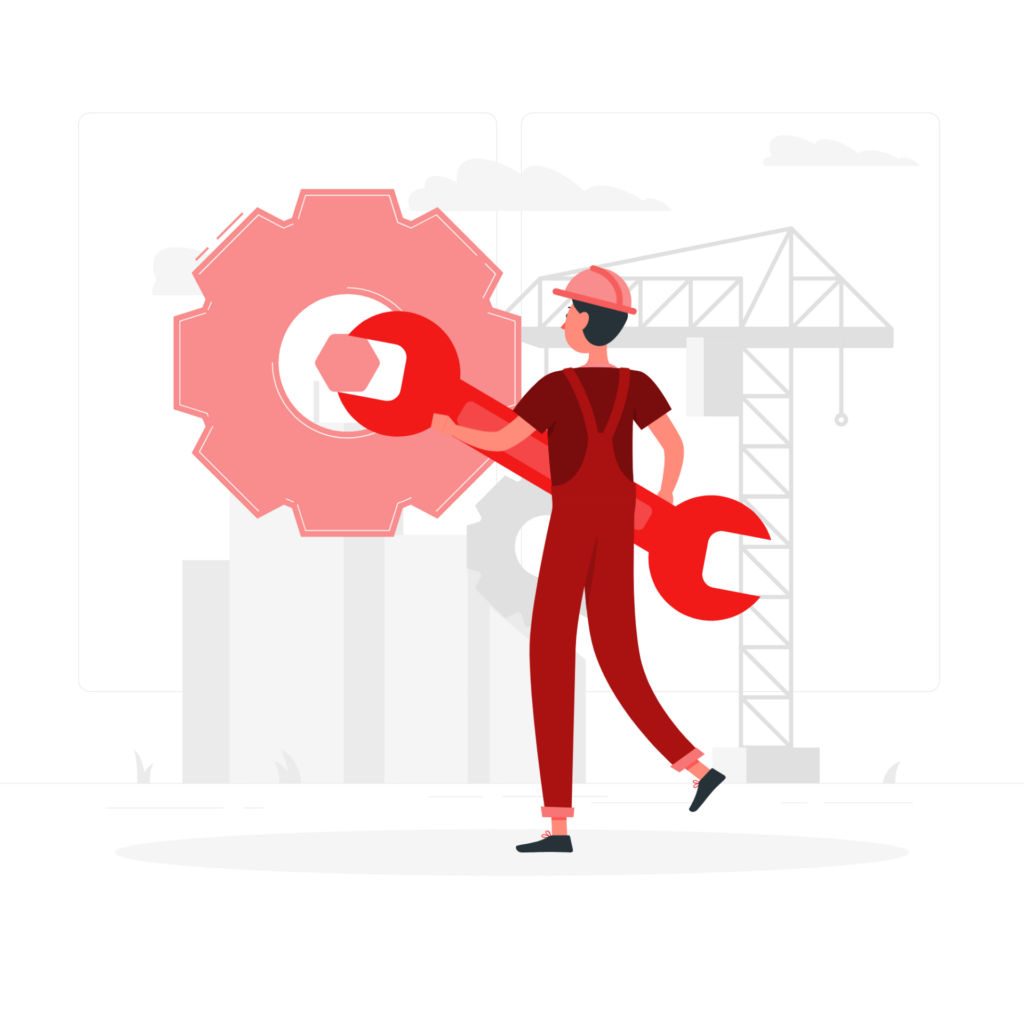
Book a free RCM Strategy Consultation tailored to your assets and industry today!