Struggling with unplanned downtime or missing spares?
Plant managers across sectors, from Oil & Gas to Manufacturing, are under constant pressure to boost asset uptime, reduce inventory bloat, and ensure compliance. Here’s a smart, often overlooked fix: asset tagging for maintenance and inventory management.
What is Asset Tagging?
Asset tagging involves assigning unique identifiers, such as barcodes, QR codes, or RFID tags, to physical assets within a facility. These tags enable real-time tracking, maintenance scheduling, and inventory control, forming the backbone of an efficient asset management system.
Why Asset Tagging Is No Longer Optional
A critical compressor fails at a petrochemical facility in Saudi Arabia. The maintenance crew scrambles, only to discover that the required spare part is untraceable. That means 48 hours of unplanned downtime and a $2 million loss.
This scenario isn’t rare. Across sectors like Oil & Gas, Manufacturing, Healthcare, and more, the inability to locate, track, and maintain critical equipment causes avoidable delays, inflated costs, and production setbacks.
That’s why asset tagging for maintenance and inventory management has become mission-critical—not optional.
By linking physical assets with digital systems through QR codes, RFID, or barcodes, companies unlock:
- Real-time visibility into asset status and location
- Predictive maintenance based on actual usage and wear
- Inventory optimization to avoid overstocking or shortages
This one step drives smarter decision-making, faster spare retrieval, and fewer maintenance delays, from control rooms in Oman to warehouses in Tamil Nadu.
Key Benefits of Asset Tagging for Maintenance and Inventory Management
Benefit | Impact |
---|---|
Real-Time Tracking | Know exactly where every asset and spare part is. |
Predictive Maintenance | Use data trends to service assets before they break down. |
Inventory Optimization | Avoid overstocking or understocking spare parts. |
Reduced Downtime | Instantly locate and verify critical equipment. |
Compliance and Auditing | Ensure traceability and documentation for audits and standards. |
Cross-Department Visibility | Share asset data across maintenance, procurement, and finance teams. |
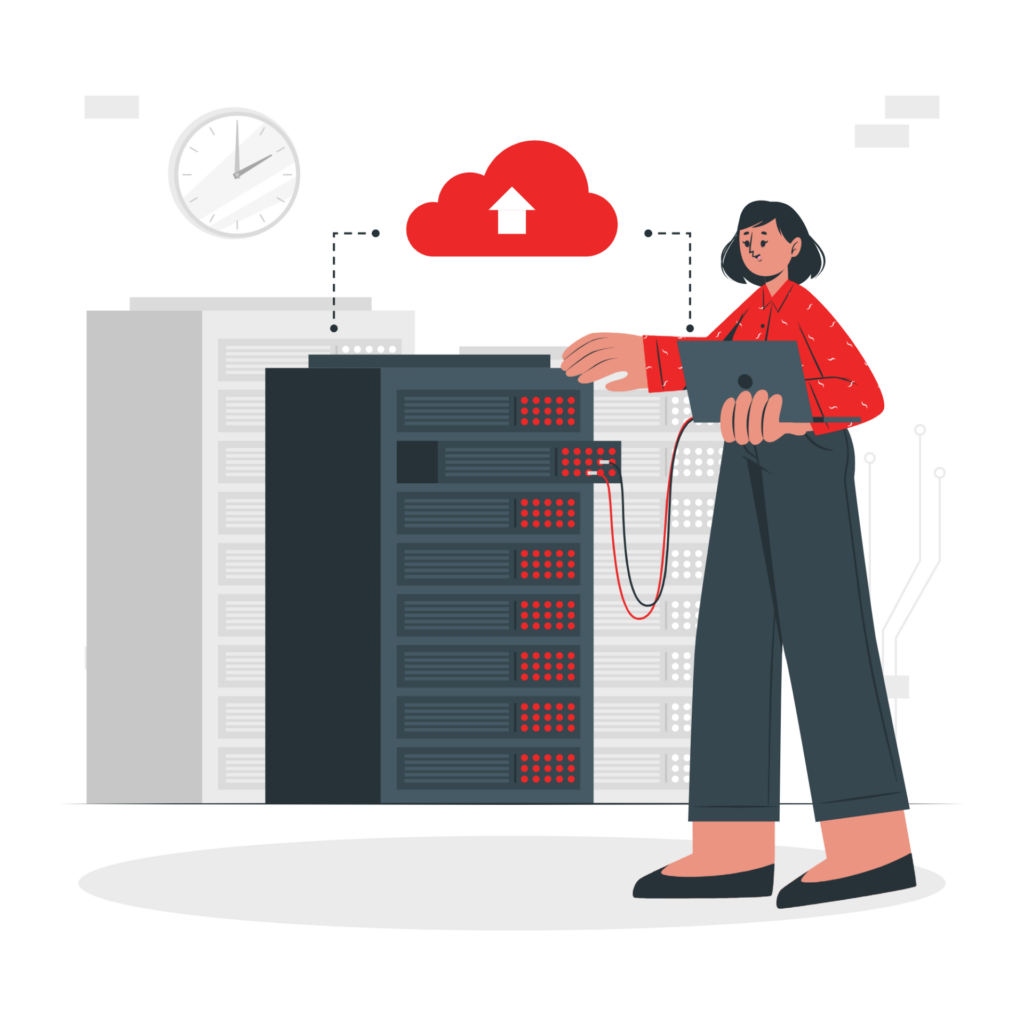
Ready to reduce downtime and improve inventory control?
Schedule a free consultation on how asset tagging can unlock savings across your plant.
How Asset Tagging Transforms Maintenance Operations
Let’s say you’re managing a power plant in Saudi Arabia or a pharma facility in India.
Every time a pump fails, your maintenance crew scrambles. But with asset tagging:
- Technicians scan the asset to retrieve its entire service history.
- Work orders auto-populate based on usage data and asset condition.
- Replacement parts are suggested instantly, pulled from tagged inventory bins.
That’s the leap from reactive firefighting to proactive, data-driven maintenance.
Use Case: Oil & Gas – Offshore Platform
- Before tagging: Teams wasted hours identifying faulty compressors and locating spares across different yards.
- After tagging: With RFID tags linked to a CMMS, time to identify and resolve issues dropped by 40%.
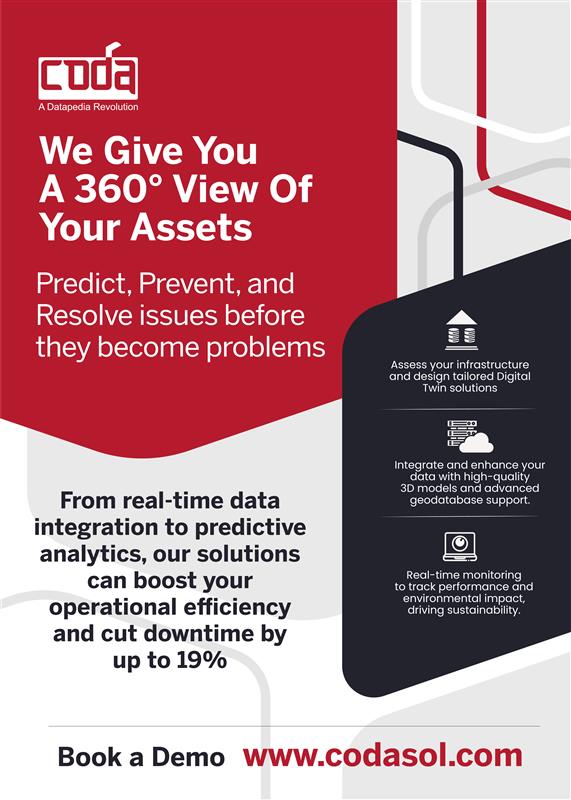
Inventory Management: Cut Waste, Not Corners
In the EPC and manufacturing world, spare part duplication is a silent profit killer.
Multiple teams ordering the same part under different names leads to:
- Overstocking
- Wasted shelf space
- Missed warranty claims
With asset tagging for inventory control:
- Every material master is digitally verified and deduplicated.
- Parts are grouped and categorized based on usage, location, and equipment.
- You build a “single source of truth” for procurement and maintenance.
This is especially useful in high-volume sectors like Healthcare, Marine & Ports, and Utilities, where asset lifecycles are long, and compliance is non-negotiable.
Best Practices for Implementing Asset Tagging
1. Start with High-Value Assets
Tag equipment that has high downtime impact or high replacement cost like turbines, pumps, HVAC units, or medical scanners.
2. Choose the Right Technology
Tag Type | Best For | Environment |
---|---|---|
Barcode | Low-cost, static assets | Clean, indoor |
QR Code | Portable assets | Light manufacturing |
RFID | High-volume or mobile tracking | Warehouses, containers |
IoT Tags | Real-time telemetry | Remote sites, utilities |
3. Integrate with CMMS or ERP
Make sure your asset tags sync with your existing system like SAP, Maximo, or Oracle. This enables auto-updates for maintenance records, spares consumption, and procurement planning.
4. Train Your Teams
Even the best tagging system fails if field teams don’t scan or update assets correctly. Invest in training and change management.
Industry-Specific Applications
Oil & Gas (GCC Region)
In the GCC, particularly in countries like UAE and Saudi Arabia, asset tagging is crucial for offshore platforms. RFID tags integrated with CMMS systems have reduced equipment identification and issue resolution times by 40%.
Healthcare (India)
Hospitals in India utilize RFID tagging for medical equipment, ensuring timely maintenance and reducing equipment downtime, thereby enhancing patient care.
Manufacturing (Far East)
Manufacturers in countries like Japan and South Korea employ QR codes for machinery, enabling efficient maintenance scheduling and minimizing production halts.
Asset Tagging Implementation Checklist
Step | Action | Why It Matters |
---|---|---|
Asset Identification | List all assets by criticality, mobility, and maintenance impact. | Focuses tagging efforts where ROI is highest. |
Define Tagging Standards | Choose between barcode, QR code, or RFID based on asset type and environment. | Ensures consistency and compatibility with future tech upgrades. |
Tag Procurement | Source durable tags (UV, chemical, and abrasion-resistant) suitable for site conditions. | Prevents tag wear-off in harsh industrial settings. |
Prepare Assets for Tagging | Clean and label surfaces; ensure accessibility for scanners. | Prevents misreads and ensures ease of maintenance. |
System Integration | Connect tags with CMMS, ERP, or MDM platforms. | Enables real-time tracking and predictive maintenance. |
Staff Training | Educate teams on scanning, data entry, and asset handling protocols. | Ensures adoption and accuracy in asset records. |
Tag & Test | Affix tags and verify data capture, linking each to the master database. | Confirms system is functioning correctly from day one. |
Audit & Validate | Conduct random checks post-tagging to validate accuracy. | Detects and corrects early-stage errors before they scale. |
Monitor & Update | Set review cycles (quarterly/annually) to update data as assets move or get replaced. | Keeps the system current, avoiding data decay. |
Continuous Improvement | Use analytics to refine tagging strategy over time. | Improves asset reliability, spare part planning, and return on investment. |
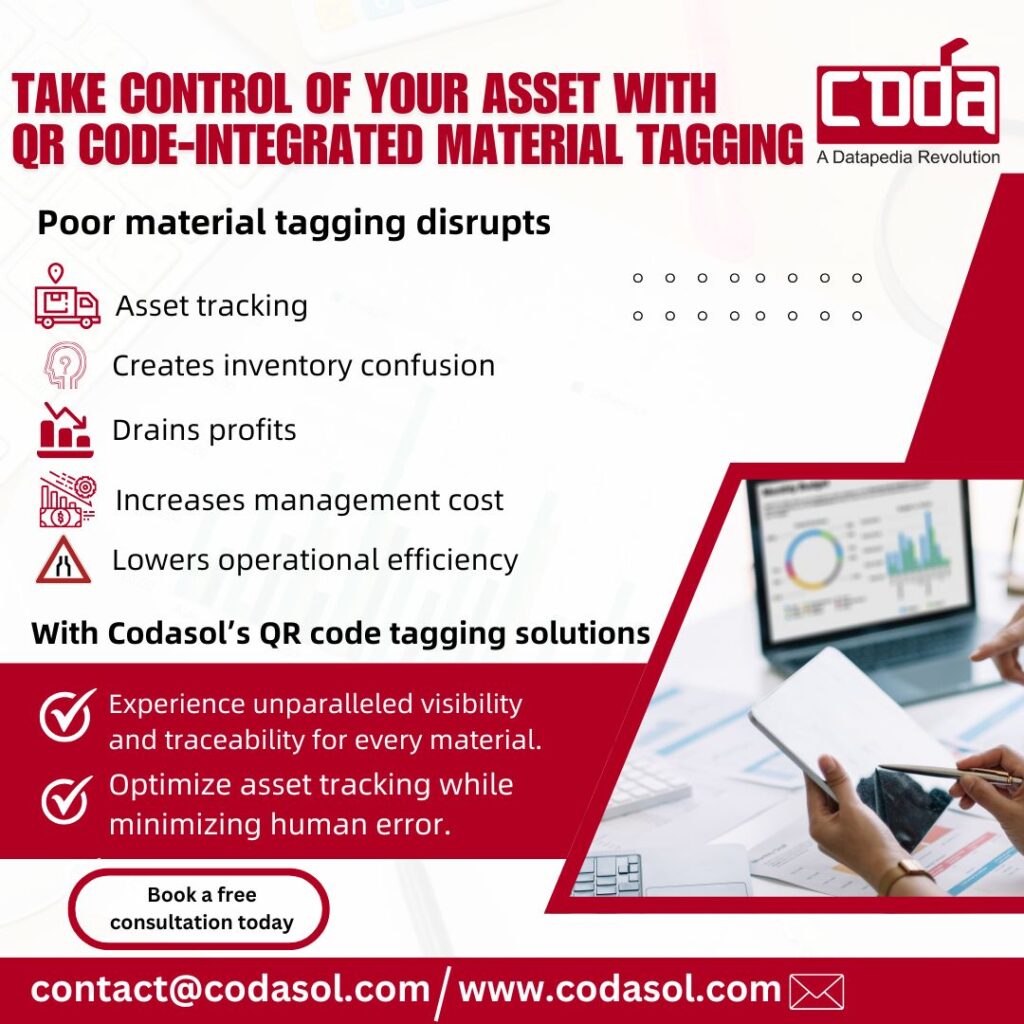
Future-Proof Your Plant with Smart Tagging
Think of asset tagging as the digital twin of your physical operations.
It gives your plant managers the visibility and control they need to:
- Prevent costly downtime
- Track critical spares in real time
- Ensure full lifecycle documentation
- Stay compliant across regions and regulations
Don’t wait for the next equipment failure. Start tagging your way to operational excellence.
Frequently Asked Questions:
1. What is asset tagging?
Asset tagging involves assigning unique identifiers (barcodes, RFID, etc.) to physical equipment and inventory to enable digital tracking and management.
2. How does asset tagging help with maintenance?
It helps technicians quickly access service history, schedule preventive maintenance, and identify the right spares, reducing downtime.
3. Which industries benefit the most from asset tagging?
Industries with large, distributed assets like Oil & Gas, Utilities, Construction, Marine, and Healthcare gain the most from tagging.
4. What systems can asset tags integrate with?
They can integrate with leading ERPs (SAP, Oracle) and CMMS platforms (IBM Maximo, Infor EAM), creating a seamless data ecosystem.
5. Is asset tagging expensive to implement?
Costs vary based on scale and technology (barcode vs. RFID vs. IoT), but ROI is high due to reduced downtime and optimized inventory.
6. Can tagging help during audits?
Yes, asset tagging ensures traceability, document availability, and proof of compliance during regulatory or financial audits.
TL;DR
- Asset tagging enhances maintenance efficiency and inventory accuracy.
- Implementation involves asset identification, appropriate tagging technology, system integration, and staff training.
- Benefits include reduced downtime, improved compliance, and streamlined operations.