If you’re the Head of Asset and Material Management, here’s the brutal truth: your assets are draining more than they’re delivering and you probably know it.
You’re battling aging equipment, costly downtimes, unpredictable failures, and duplicate materials across warehouses. But what if a strategic approach to maximizing asset lifecycle management could flip that equation?
Let’s dive into what works, what doesn’t, and how you can gain control with insights you can act on today.
What Is Asset Lifecycle Management?
Asset Lifecycle Management (ALM) is the structured approach to managing an asset from acquisition to disposal. It’s about optimizing the performance, cost, and lifespan of physical assets across every phase:
- Plan & Design
- Procure & Install
- Operate & Maintain
- Decommission & Dispose
Why It Matters More Now Than Ever
In industries like Oil & Gas, Utilities, EPC, and Manufacturing, assets are capital-intensive. Poor lifecycle management can lead to:
- 25–40% higher operational costs
- 10–30% avoidable downtime
- Underutilized inventories worth millions
Case study:
- A utility firm in UAE had 150,000 line items in their material master.
- A de-duplication audit revealed 18% were redundant.
- Removing duplicates saved $3.2M in working capital
- Reduced search time by 30%.
Key Challenges for Asset Heads Today
Challenge | Impact |
---|---|
Fragmented asset data | Poor visibility & decisions |
Manual maintenance planning | Unplanned downtime |
Obsolete spare parts | Delayed repairs, increased costs |
Siloed ERP & EAM systems | Inefficiencies across procurement and warehousing |
Lack of predictive analytics | Reactive rather than proactive asset strategies |
7 Strategies to Maximize Asset Lifecycle Management
1. Centralize Asset Data with a Single Source of Truth
A unified view of your assets starts with clean, enriched material and equipment master data. Ensure consistency across SAP, Oracle, Maximo, or any ERP system.
2. Implement Predictive Maintenance
Use IoT sensors and AI to anticipate failures before they happen. This reduces:
- Emergency repairs
- Spare part stockouts
- Downtime penalties
3. Use BOM and Spares Optimization
Bill of Materials (BOM) clarity avoids overstocking and hoarding of redundant spares.
Example: A construction firm in Saudi Arabia reduced 12% of inventory after aligning spare parts with actual equipment BOMs.
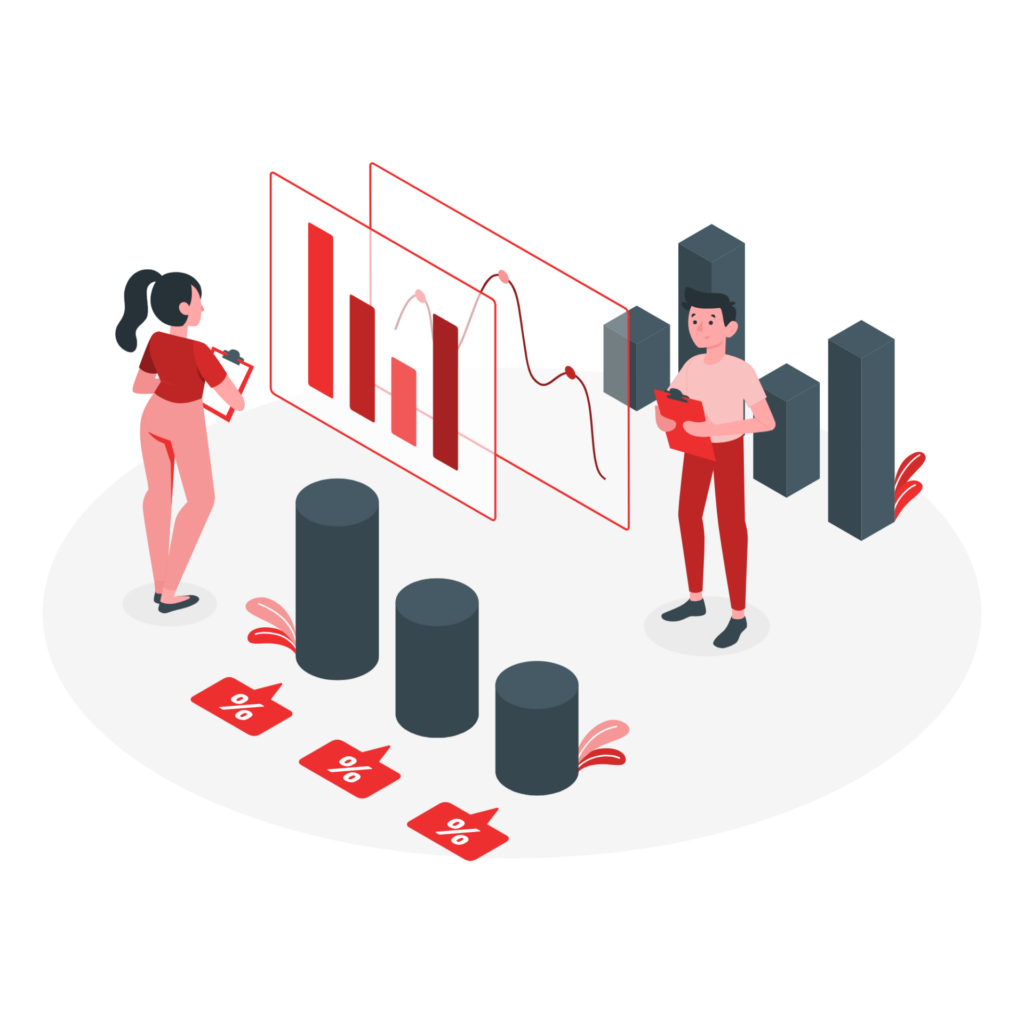
Get Your Free Asset Lifecycle Audit
Discover where your gaps are and how much you can save with a quick 15-minute consultation.
4. Leverage De-duplication Algorithms
Eliminate duplicate material entries that inflate inventory value and confuse procurement.
A company in South Korea saved $4.5M by de-duplicating 100,000+ material line items across 5 sites.
5. Adopt Lifecycle Costing (LCC) Models
Don’t just consider purchase cost. Factor in operating, maintenance, and disposal costs. LCC allows better vendor comparison and long-term asset value planning.
6. Integrate EAM with Procurement & Finance
Create synergy across departments with synchronized workflows and alerts. When engineering changes asset specs, procurement should auto-adjust sourcing policies.
7. Use Digital Twins for High-CapEx Assets
Simulate asset behavior digitally to optimize maintenance intervals and predict performance outcomes under various scenarios.
Key Benefits of Strategic Lifecycle Management
- Longer asset uptime
- Lower total cost of ownership
- Faster procurement turnaround
- Accurate forecasting of spare parts
- Improved regulatory compliance
Lifecycle Phase vs Optimization Techniques
Phase | Optimization Strategy | Tools/Techniques |
---|---|---|
Design | Lifecycle Costing, Asset Specs Optimization | LCC models, Digital Twins |
Procurement | Vendor Rationalization, Spares Standardization | Spend Analytics, MDM Platforms |
Operation | Predictive Maintenance, KPI Monitoring | IoT Sensors, AI/ML |
Maintenance | Spare Parts Planning, BOM Accuracy | EAM, Maintenance Schedulers |
Decommissioning | Cost Recovery, Scrap Value Realization | Disposal Planning Tools, Asset Audits |
Frequently Asked Questions
1: How can predictive maintenance increase ROI?
It reduces unscheduled downtimes and prolongs asset life, lowering repair and replacement costs.
2: What is lifecycle costing in asset management?
Lifecycle costing evaluates the total cost of ownership including purchase, maintenance, operation, and disposal helping in smarter procurement.
3: How do I know if I have duplicate materials?
Run a de-duplication audit across your material master. Platforms like PROSOL can identify similar entries using AI.
4: Which industries benefit most from lifecycle management?
Any asset-intensive industry including Oil & Gas, Utilities, EPC, Marine, Healthcare, and Manufacturing.
5: How long does it take to implement a lifecycle strategy?
Depending on scope and readiness, it can range from 2 weeks (data audit) to 6–12 months (full system integration).
Final Thoughts
If you’re in charge of assets in India, GCC, Far East, or the US, this is the time to ditch reactive practices. Modern lifecycle management isn’t just about keeping things running, it’s about boosting returns from what you already own.
By strategically focusing on data, digital tools, and proactive planning, you unlock massive hidden value in your infrastructure.
Ready to make your asset lifecycle work for you?
Is your asset data holding you back?
Clean data = better performance. Start with a free Material Master Health Check.
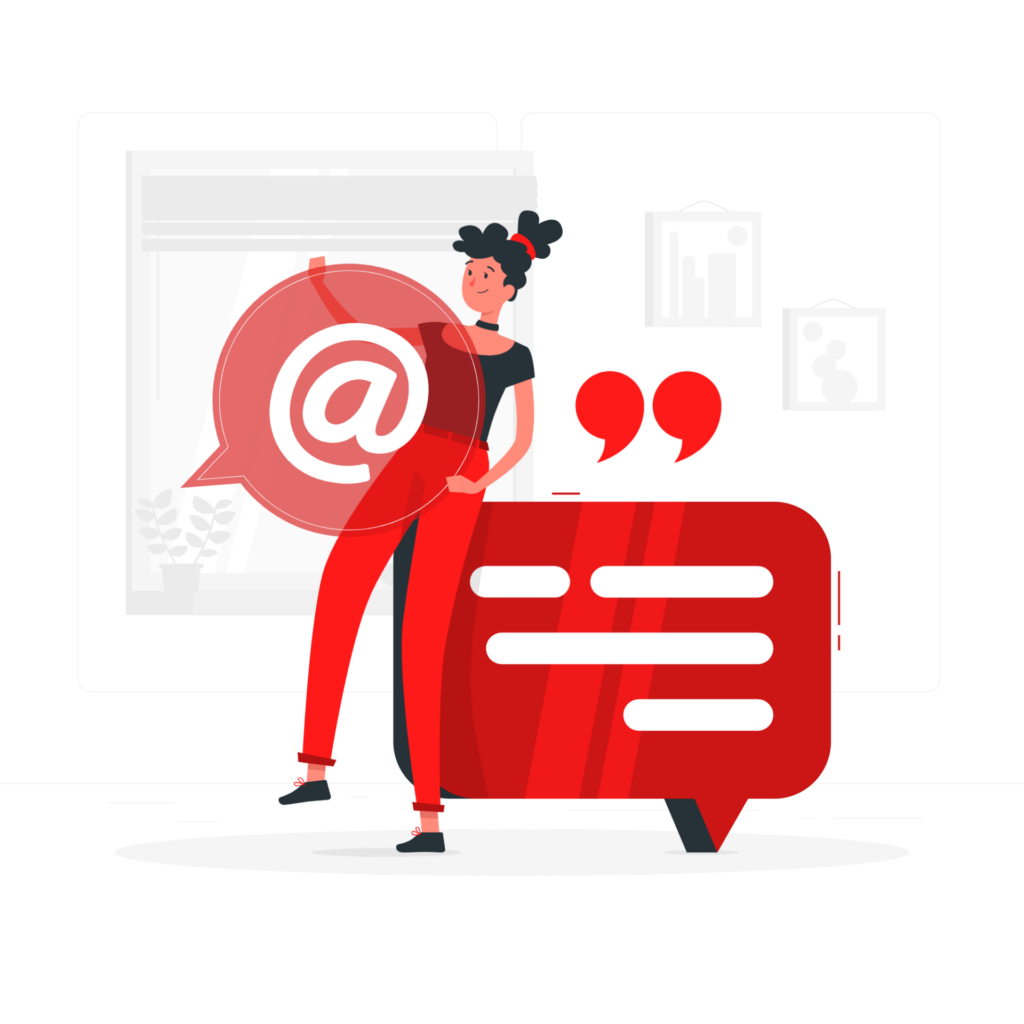