Asset Tagging for Brownfield Plants: Where to Start and What to Avoid
Let’s be honest. Most brownfield plants weren’t built with digital transformation in mind. Rows of aging equipment, inconsistent documentation, and a mix of legacy and modern systems make asset tagging feel like untangling a giant ball of yarn.
Yet, without accurate asset tagging, your digital initiatives, be it preventive maintenance, digital twins, or even ERP integration, are flying blind.
So where do you even begin?
This guide is for plant heads, reliability engineers, and IT managers staring at a mess of assets, asking one burning question: “How do we tag what we don’t fully understand?”
What Is Asset Tagging (And Why Brownfield Makes It Tricky)?
Asset tagging is assigning a unique identifier to every physical asset so it can be tracked, maintained, and analyzed. These tags can be QR codes, RFID, barcodes, or alphanumeric IDs.
In a greenfield setup, tagging is simple. You build; you tag. In brownfield environments, however:
- Equipment may not have a standard naming convention
- Documentation is outdated (or missing!)
- Assets may have been modified without records
- Mismatched vendor data adds further complexity
So, while tagging sounds basic, executing it in a brownfield site without a plan is a recipe for chaos.
Where to Start: The 5-Step Framework
Here’s a clear roadmap that even a non-technical stakeholder can follow:
1. Audit What You Have
Start with a physical verification walkdown. Categorize assets into:
- Critical vs. non-critical
- Static vs. rotating
- Tagged vs. untagged
Use this opportunity to:
- Cross-check BOMs and P&IDs
- Note missing or duplicated data
“You can’t tag what you don’t see.”
2. Clean the Data
Before slapping tags on anything, clean up the asset master. This step includes:
- Deduplication
- Standardizing naming conventions
- Filling in missing fields like location, make, model, serial number
This is where Master Data Management (MDM) platforms shine. For example, solutions like PROSOL auto-suggest standard terms and flag inconsistencies using AI.
Explore PROSOL’s capabilities listed in the SAP Store to see how it integrates seamlessly with your existing ERP.
3. Define Your Tagging Strategy
Choose your tagging method based on:
- Environmental factors (QR codes fade in outdoor plants)
- Mobility needs (RFID helps for real-time tracking)
- Integration goals (with SAP, Maximo, etc.)
Also define:
- Tag formats (e.g., EQUIP-0001, LOC-0023)
- Color coding or asset class differentiation
4. Deploy Smartly – Prioritize Critical Assets
You don’t have to tag everything on Day 1. Instead:
- Start with critical rotating equipment
- Use pilot zones to test
- Train maintenance and inventory teams concurrently
This is where tools like i-Stock, CODASOL’s mobile-first asset tagging and inventory app, can make a huge difference. i-Stock allows you to:
- Tag assets in real time using QR, barcode, or RFID
- Capture geolocation, photos, and condition status during physical verification
- Sync directly with ERP systems and MDM platforms like PROSOL
- Work offline in remote plant environments and sync when connected
It’s built for brownfield complexity, letting you deploy faster without compromising accuracy.
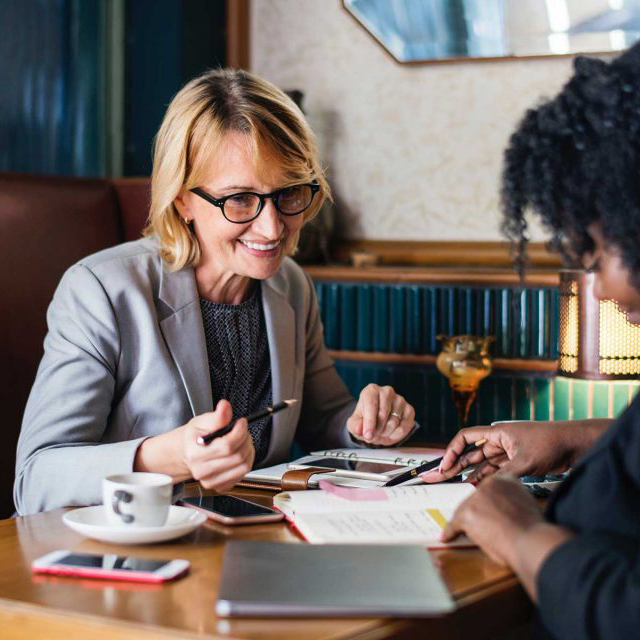
Let our experts walk your plant and build a tagging roadmap tailored to your goals. Try i-Stock for a hands-on demo and see how fast tagging can really get.
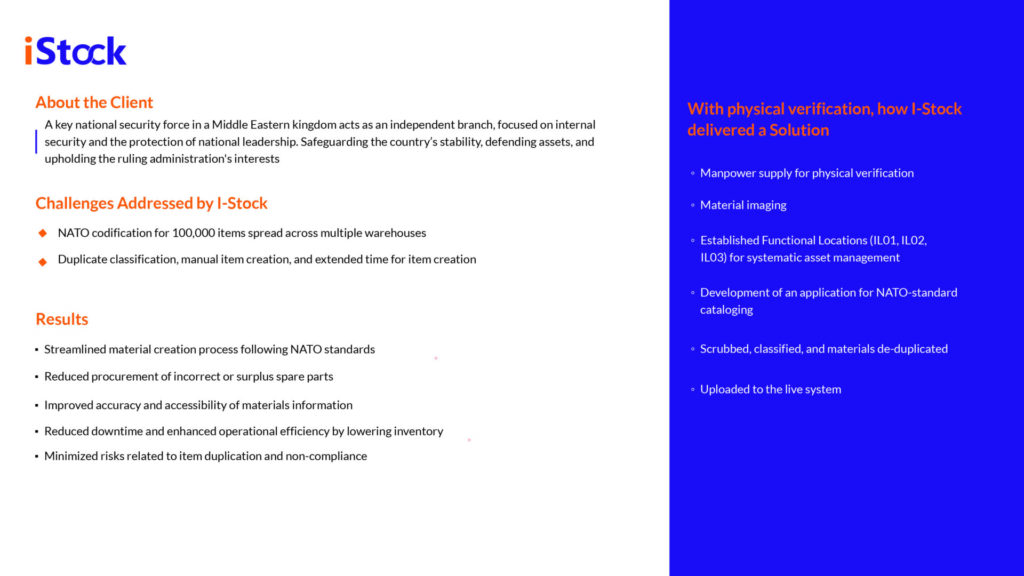
5. Integrate with Existing Systems
Finally, link the tagged assets with your:
- ERP system (SAP, Oracle, Maximo)
- Maintenance software (CMMS)
- Engineering documents and digital twins
This ensures the tags aren’t just stickers but data enablers.
What to Avoid: Common Mistakes That Can Cost You
1. Tagging Before Cleansing:
Adding tags without cleaning your asset data only digitizes bad information.
2. One-Size-Fits-All Tagging:
RFID doesn’t work well in metal-heavy environments. QR codes fade outdoors. Choose wisely.
3. Ignoring Change Management:
If your teams aren’t trained to use the new tags or systems, the project will stall post-deployment.
4. Skipping Governance:
Without clear ownership of asset data updates, it will soon become unreliable again.
5. No Scalability Plan:
Pilot projects that don’t plan for scale often end up as isolated islands of data.
Case study
Industry: Utilities | Region: GCC
A mid-sized desalination plant in Oman had over 12,000 untagged assets. Their spare parts inventory had over 30% duplicates, causing delays and unnecessary procurement.
By:
- Auditing and standardizing 100% of equipment data
- Applying RFID tagging for critical pumps and valves
- Integrating tags with their SAP PM module
They cut maintenance response time by 18% and reduced duplicate inventory by 22% within 6 months.
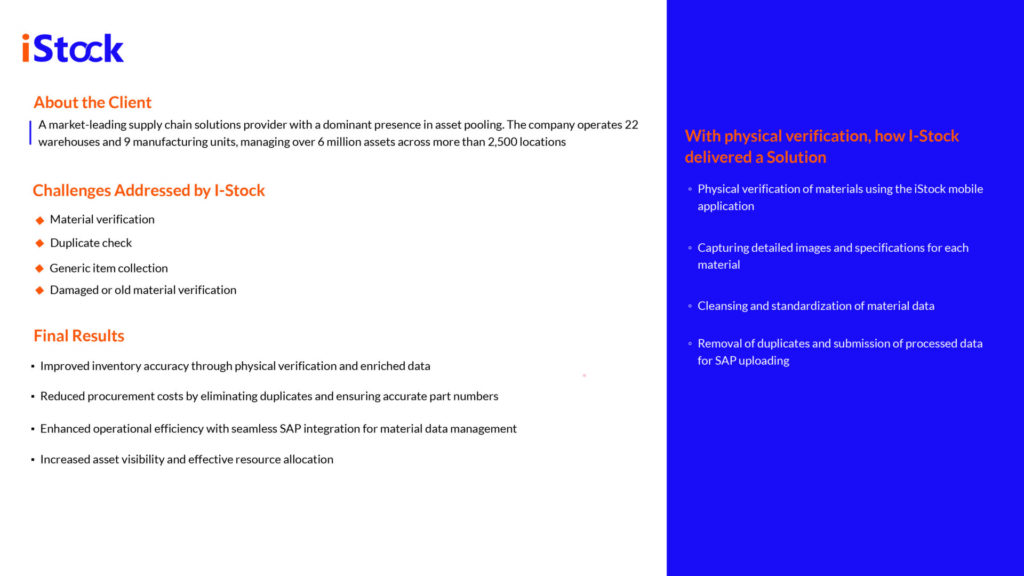
Tagging Method Comparison for Brownfield Plants
Tag Type | Cost | Best For | Limitations |
---|---|---|---|
QR Code | Low | Indoor assets | Fades in sunlight, needs manual scan |
RFID | Medium | High-mobility or critical equipment | Needs readers, signal issues in metals |
Barcode | Low | Fixed, low-risk assets | Manual scan, less data rich |
Alphanumeric ID | Minimal | Documentation and backups | Not machine-readable |
FAQs
1. How long does asset tagging take in brownfield plants?
Depends on plant size and complexity. A phased approach across zones typically takes 3–9 months.
2. Is asset tagging only for maintenance?
No. It also benefits procurement, safety audits, inventory planning, and digital transformation initiatives.
3. How often should tags be updated or reviewed?
Every 6–12 months, or after major maintenance or shutdowns.
4. Do we need a full MDM platform to start tagging?
No, but MDM accelerates accuracy and integration. Manual approaches work for small pilots.
5. Can tags be reused for new assets?
Technically yes, but it’s best to use new identifiers to maintain traceability.
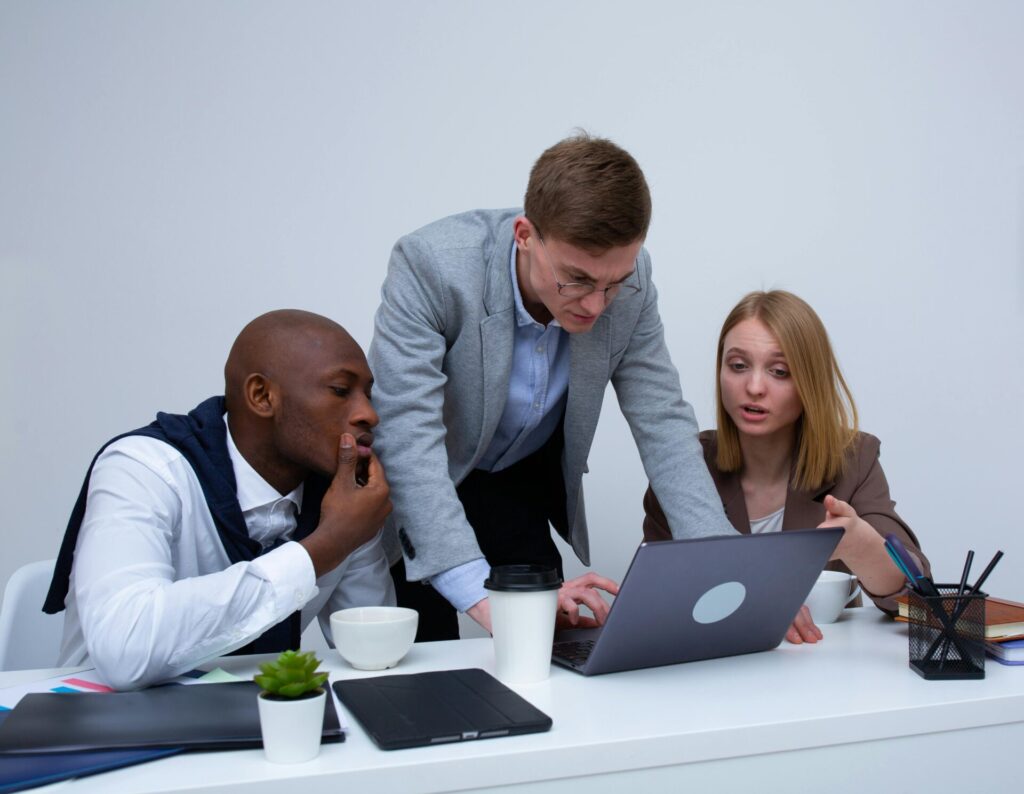
Want a Scalable Asset Tagging Solution?
See how i-Stock and PROSOL work together to make brownfield asset tagging fast, accurate, and future-ready.
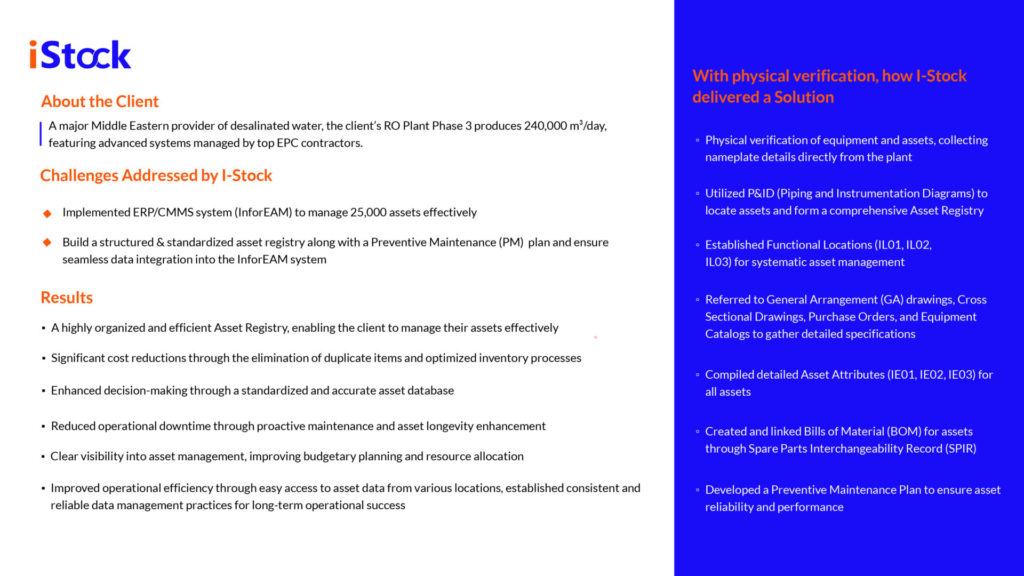