You’re losing money every day without realizing it. Idle inventory, duplication, poor visibility, and inefficient procurement drain your enterprise’s resources. If you’re a Head of Operations in industries like Oil & Gas, Utilities, EPC, Healthcare, or Aviation, this post will show you how to take control and stop these losses.
Why Inventory Management Is a Hidden ROI Lever
In large-scale operations, inventory is both a strategic asset and a liability. Poor inventory practices lead to:
- Overstocking: Wasted capital tied up in slow-moving or obsolete items.
- Understocking: Costly delays due to unavailable critical spares.
- Duplication: Unnecessary purchases due to inconsistent naming and categorization.
- Lack of Visibility: Disjointed systems and poor data leading to procurement chaos.
According to McKinsey, companies that focus on inventory visibility and optimization can reduce inventory holding costs by up to 25% and improve service levels by 30%.
The High-Stakes Challenge for Operations Leaders
Managing inventory across large sites, complex supply chains, and multi-country operations (like in India, GCC, Far East, or the US) brings specific challenges:
- Thousands of SKUs across categories like MRO, safety, equipment spares
- Decentralized warehouses and legacy ERP systems
- Emergency procurement causing inflated costs
- Fragmented vendor databases
- Compliance with local tax, import/export, and safety regulations
You don’t just need inventory management. You need inventory intelligence.
Need to cut your inventory costs by 20% this year?
Request a personalized Inventory Audit for your operations in India, GCC, the US, or the Far East.
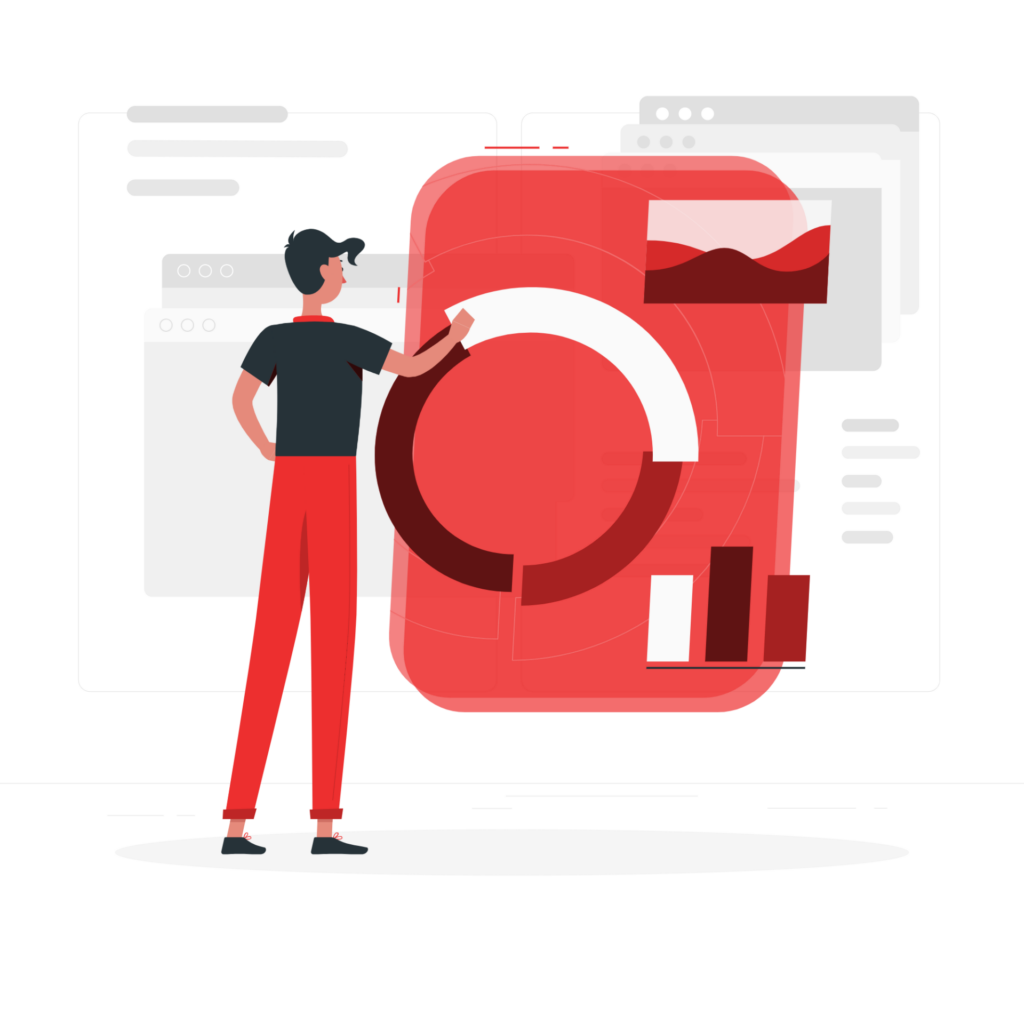
Inventory Optimization Framework for Large-Scale Operations
Area | Problem | Optimization Solution |
---|---|---|
Data | Duplicate and unstructured material master | Master Data Management (MDM), AI-based deduplication |
Visibility | Poor SKU tracking across multiple locations | Digital dashboards and IoT-enabled tracking |
Procurement | High costs due to emergency or redundant purchases | Spend analytics, Vendor consolidation |
Operations | Stockouts disrupting production | Minimum-Maximum (Min-Max) policies with predictive analytics |
Capital | Excess capital blocked in inventory | ABC analysis, criticality mapping |
Proven Strategies to Drive Inventory Efficiency
1. Master Data Standardization with AI/ML
Large organizations typically have 10–20% duplication in their material master. Inaccurate descriptions or multiple naming conventions (e.g., “Bolt – 12mm” vs. “12mm Bolt”) lead to redundant procurement.
Solution: Implement a centralized MDM platform powered by AI/ML. This automatically cleanses, deduplicates, and enriches your material master. CODASOL’s PROSOL, for instance, helped one utility firm in the GCC reduce 15% of redundant inventory, saving $3.2 million annually.
2. Min-Max Optimization with Real-Time Monitoring
Using real-time usage data, set dynamic reorder levels. This minimizes both stockouts and overstocking.
Example: A hospital in India optimized its critical-care inventory using real-time usage data, cutting emergency orders by 35%.
3. Inventory Categorization Using ABC-VED-Criticality Models
Group items based on value (ABC), criticality (VED), and usage frequency. Focus resources on what truly matters.
- A-items: High-value, low-quantity (tight control)
- B-items: Moderate value (scheduled review)
- C-items: Low-value (bulk purchase or consignment)
4. Centralized Procurement with Vendor Rationalization
Consolidate vendors to increase negotiation power, improve quality, and streamline logistics.
Use Case: An EPC firm operating in Qatar and Oman reduced procurement lead time by 40% after moving from 3,200 vendors to 1,100 vetted partners.
5. Digital Inventory Audits with Drones and IoT
For sectors like Real Estate, Ports, and Construction, drone-based audits paired with RFID tagging reduce manual errors and offer a bird’s-eye view of stock positioning.
Key Technologies Driving Inventory Optimization
- Master Data Management (MDM) Tools – Like PROSOL, offering ERP integration
- AI/ML Algorithms – For pattern detection and predictive restocking
- IoT Devices – For real-time location and condition monitoring
- Cloud Dashboards – For cross-site visibility and analytics
- Robotic Process Automation (RPA) – For auto-replenishment triggers and reporting
Industries Benefiting from Inventory Optimization
Whether it’s valves for an offshore platform or stents in a hospital, better inventory management improves both efficiency and profitability.
Industry | Inventory Impact | Potential Optimization |
---|---|---|
Oil & Gas | Long lead times, critical spares | Predictive stocking, vendor-backed consignment |
Utilities | Aging infrastructure, legacy parts | MDM, ABC-VED classification |
Manufacturing | WIP disruptions | Just-in-time (JIT) inventory, Min-Max |
Healthcare | Lifesaving item availability | Auto-replenishment via consumption trends |
Marine & Ports | Complex warehousing | RFID & digital audits |
Real Estate | Construction material delays | Centralized procurement |
Banking | Facility management supplies | Demand forecasting |
Government | Compliance-heavy procurement | Transparent inventory policies |
EPC | Cross-country logistics | Unified vendor management |
The Cost of Inaction
Example: A steel plant in the Far East region had a duplicated inventory worth $4.8M. After a 6-month MDM project, 18% of SKUs were eliminated, saving $860,000 in procurement and storage costs.
Let’s say your average material cost is $300 and you have 100,000 SKUs.
- 12% duplication = 12,000 redundant items
- $300 x 12,000 = $3.6 million in blocked capital
- With optimization, ROI in 6–8 months is achievable.
Frequently Answered Questions
1. What is the best inventory optimization model for critical industries?
A hybrid model combining ABC, VED, and criticality analysis with AI-based forecasting yields the best results.
2. How do I start an MDM project for inventory?
Begin with a material master audit, identify duplicates and inconsistencies, then deploy an AI/ML-based cleansing and standardization tool.
3. What industries benefit most from inventory optimization?
Industries with high-value or high-risk inventory, such as Oil and gas, EPC, Healthcare, and Aviation, see the fastest ROI.
4. Can small or mid-sized operations also benefit?
Absolutely. Even a 10% efficiency gain in smaller setups can free significant working capital.
5. How can we reduce emergency procurement?
By using predictive analytics to identify usage patterns and ensure timely reordering of critical parts.
Final Thoughts
Optimizing inventory management for large-scale operations isn’t just about reducing costs, it’s about enabling agility, preventing downtime, and freeing capital for innovation. If you’re leading operations in Oil & Gas, Utilities, EPC, or Healthcare, take the first step now. Because the real cost is in waiting.
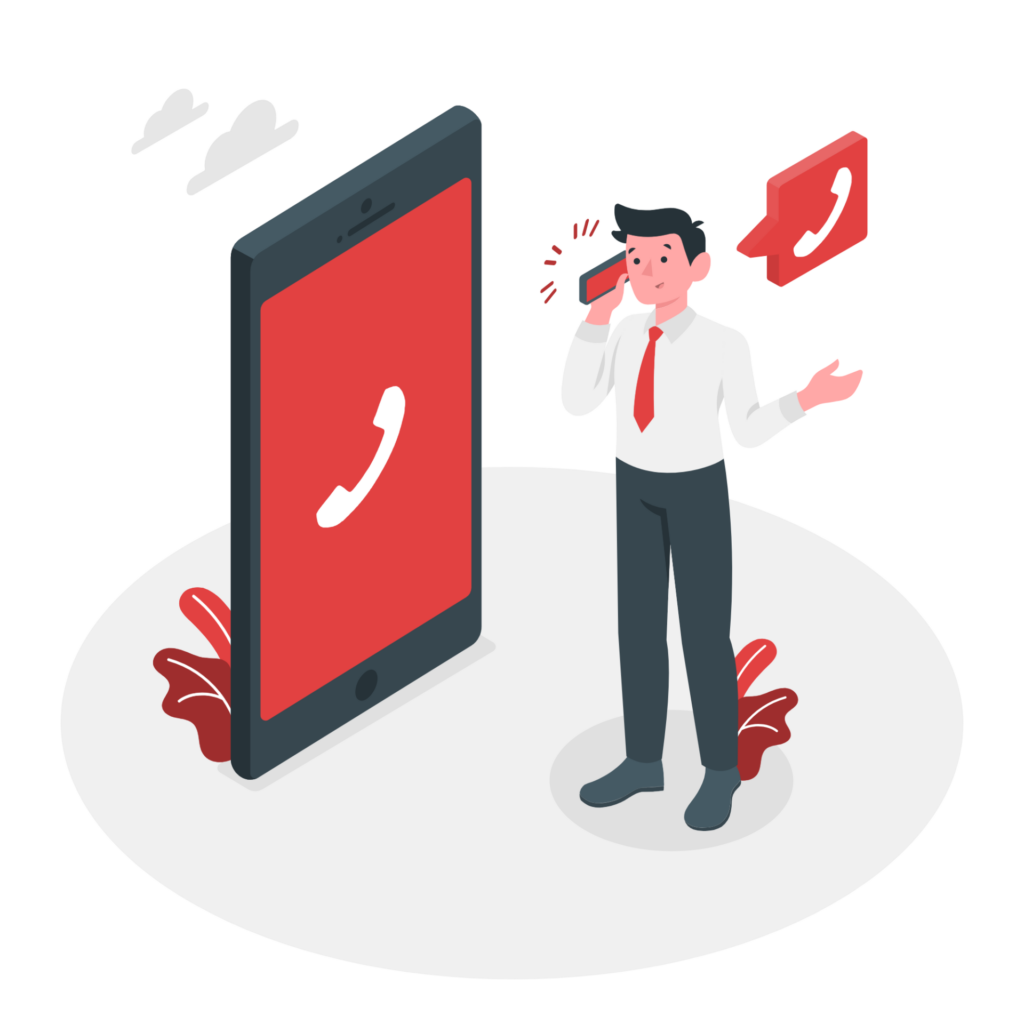
Transform Inventory from a Cost Center to a Strategic Asset
See how leading organizations are leveraging AI-driven inventory management for real ROI.